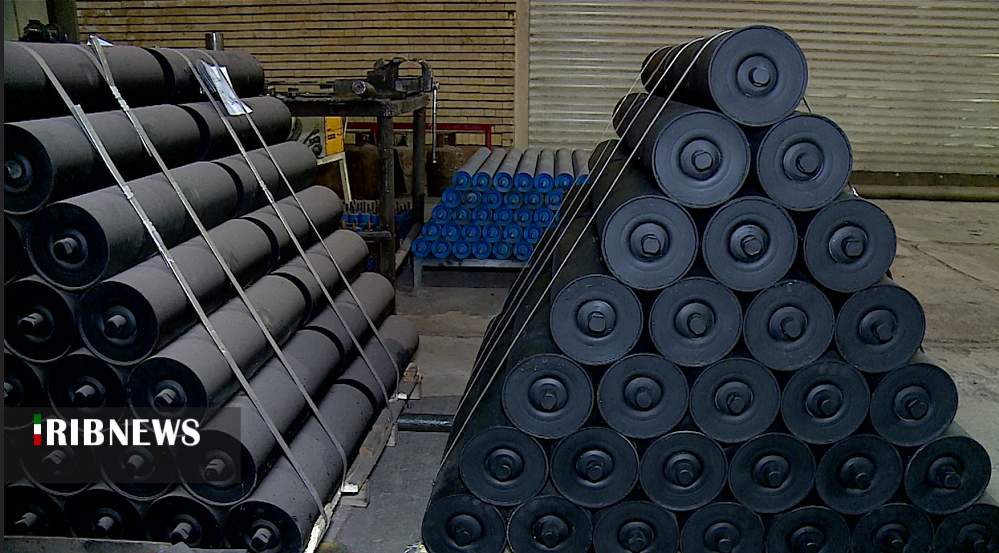
به
گزارش خبرگزاری صداوسیما مرکز آذربایجان شرقی، این وقفه می تواند زیر سر نبود یک پیچ مهره بندانگشتی باشد، یا ساییدگی یک سازه چند صد تنی در گذر زمان.
اینجا سکوت کوهستان و غرور سنگ ها را یا دامپ تراک های غول پیکر " کامیون های معدنی" زیر چرخ های خود می شکنند، یا انفجارهای گاه و بی گاه، راز دل سنگ های معدن مس سونگون را فاش می کند.
سونگون، دومین ذخیره معدنی مس کشورمعدنی که از لحاظ وسعت و بزرگی، با ذخیره افزون بر یک میلیارد و 350 میلیون تن، بعد از معدن مس سرچشمه، دومین ذخیره مس ایران محسوب می شود.
به گفته شاهوردی رئیس معدن، محدوده اکتشافی در این معدن یک 8 ضلعی به مساحت 38 کیلومترمربع است، بلندترین نقطه از معدن، ارتفاع 2 هزار و 400 متری و نقطه انتهایی آن یک هزار و 600 متر مربع است در واقع در گستره 800 متر از سینه این کوه، ماده معدنی وجود دارد.
در اهمیت مجتمع مس سونگون همین بس که جزء 40 معدن بزرگ دنیا است و با تولید 320 هزار تن کنسانتره مس، با عیار 24.5 درصد حدود 30 درصد کنسانتره ی تولیدی کشور را تولید می کند.
از بالا و خارج از گودی، به "کلوسئوم" میدان نبرد گلادیاتورهای رومی شبیه است؛ حالت پلکانی دارد، ارتفاع پله ها هم یک دست است.
قبلا کوه بوده و به مرور و با گسترده شدن اکتشافات در منطقه، این گودی عریض و عمیق تر شده است.
سنگ های اینجا از نوع "کوارتز مونزونیت" پورفیری است و به دوره سوم زمین شناسی برمی گردد، که در مجاورت آهک های دوره دوم زمین شناسی، توده های پورفیری تشکیل شده اند.
عیار کل مس در این معدن 58 صدم درصد است اما آنچه که از زمین برداشت می شود، عیار 63 صدم درصد است.
رئیس معدن می افزاید: این معدن از لحاظ زمین شناسی جزء معادن پیچیده دنیا محسوب می شود چرا که تیپ های مختلف ماده های معدنی به صورت تزریقی و نه رگه ای در منطقه وجود دارد و در هم رفتگی باطله و مواد معدنی به قدری بالا است که استخراج را با مشکل مواجه می کند.
در معدنی که کار در آن تعطیلی بردار نیست، در سال 14 میلیون تن ماده معدنی به کارخانه ارسال می شود و در نتیجه آن 300 هزار تن کنسانتره با عیار 25 درصد تولید می شود.
پای تجهیزات خارجی، از صنعت مس کوتاه می شودتنوع سنگ و پورفیری بودن معدن، کار اکتشاف را سخت می کند، اما آنچه می تواند معدن را به تعطیلی بکشاند، تجهیزاتی است که چند وقتی است، با تیغ تحریم ها کند شده اند.
آری! شرکت ملی صنایع مس ایران جز شرکت هایی است که چوب تحریم را می خورد و قرار بود صنعت مس نیز، با همین سنگ تحریم، روزنه ای برای پیشرفت نداشته باشد و چرخ ها از دور حرکت باز بایستند.
در این شرایط تنها گزینه ای که روی میز مدیران شرکت صنایع ملی مس ایران قرار گرفت، کم کردن وابستگی ها به خارج بود تا بتوانند خاک مس را طلا کنند.
آنچه از شواهد بر می آید، هم اکنون و بعد از تشدید تحریم ها، پای خیلی از تجهیزاتی که قرار بود با به موقع نرسیدن و دیر رسیدن شان، دست صنعت مس را در حنا بگذارند، از این صنعت کوتاه شده است.
45 درصد قطعات بومی سازی شده استتا جایی که به گفته بیات مدیر عامل مجتمع مس سونگون، اکنون 45 درصد از قطعاتی که در مجموعه استفاده می شود ساخت داخل و بومی سازی شده است.
برای مثال بیات مدیر عامل شرکت مجتمع مس سونگون می گوید: در این مجتمع از 1400 قلم کالای وارداتی در چند سال پیش، هم اکنون به 50 قلم رسیده ایم، این یعنی تنزل جایگاه اقلام وارداتی در سبد خرید صنعت مس.
فقط برای اینکه چرخ های این مجتمع بچرخد، 7 هزار و 500 قلم قطعه از اندازه بند انگشتی گرفته تا قطعات چند تنی با هم ترکیب شده اند که اکنون 5 هزار و 500 قطعه بومی سازی شده و بقیه اقلام مورد نیاز نیز، به ترتیب برای ساخت به شرکت های داخلی واگذار می شود.
برای تحقق این آمار و ارقام، و نجات صنعت مس از باتلاقی که تحریم تدارک دیده بود، چاره ای جز استفاده از پتانسیل ساخت داخل وجود نداشت، و باید سازندگان جدید شناسایی و در فرآیند ساخت از آنها کمک گرفته می شد.
صنعت امروز، با نسخه 10 سال پیش، پیش نمی رودالبته با قبول این پیش فرض که با فرآیندها و نسخه 10 سال پیش نمی توان صنعت امروزی را اداره کرد لذا لازم است قوانین و فرایندها متناسب با شرایط اقتصادی بازطراحی شود.
بیشترین توان برای تامین و تدارک تجیهزات این مجتمع بر دوش مدیریت بازرگانی منطقه آذربایجان شرکت ملی مس ایران قرار گرفت.
واحدی که در سه محور خرید داخل، خرید خارج و ساخت داخل همزمان خدمات ارائه می دهد و سیاست هایش بر دو اصل حمایت از ساخت داخل در قالب نهضت ساخت داخل و منطقه گرایی متمرکز است.
آغاز نهضت ساخت داخل با تاکید برمنطقه گراییبراساس همین 2 اصل که از طرف برنامه راهبردی وزارت صمت اعلام شده، کاهش خرید خارجی و به نسبت آن تامین قطعات از داخل، آنهم در قالب کارگاههای ساخت داخل انجام می شود.
بررسی نمودارها نشان می دهد: اگر سال 91 حدود 352 قطعه برای پایداری خط تولید سونگون ساخته شده بود، این نمودار در سال 95 ساخت 748 قطعه را نشان می دهد و سال 98 حدود 959 قطعه با مشارکت سازندگان منطقه و کشور ساخته شد.
نقطه عطف این نمودار ها به سال گذشته مربوط می شود، سال گذشته 1500 قطعه، هم ردیف با خرید خارجی در قالب سیاست ساخت داخل، در دستور کار ساخت داخل قرار گرفت.
از این یک هزار و 500 قطعه در یک سال اخیر، نقشه 810 قطعه تهیه و وارد فرایند ساخت شده و در 11 ماهه امسال 878 قطعه از سازندگان کشور تامین و برای پایداری خط تولید مجتمع مس سونگون استفاده می شود.
رشد سهم شرکت های استانی از 5 به 46 درصدبه صورت ویژه از سال 91 سیاست ساخت داخل یا تامین قطعات از محل ساخت داخل مجتمع سونگون شروع شد، اما در این مدت سیاست منطقه گرایی بیشتر زیر زبان مدیریت مجتمع مس سونگون مزه کرده است.
نشان به آن نشان که سال 96 سهم منطقه آذربایجان از کل ساخت ها 5 درصد بود و برپایه ی سیاست منطقه گرایی سال 98 این رقم به 38 درصد و امروز این آمار به 46 درصد رسیده است یعنی 46 درصد از این قطعات از طریق سازندگان قطعات آذربایجان شرقی و منطقه ساخت شده است.
از مجموع یک هزار و 540 آیتم درخواست های خرید خارجی که وارد چرخه ساخت در کارگروه توسعه ساخت داخل شده، بالغ بر 75 درصد به سازندگان ابلاغ شده و در حال ساخت است.
در واحد ساخت معاونت بازرگانی مس آذربایجان در حال حاضر، حدود 460 آیتم درخواست خارجی در حال ساخت است که از این تعداد، 300 آیتم برای بار اول مستندات فنی تهیه و در حال تکمیل فرایند هستند.
سرند ارتعاشی؛ هم تراز با نمونه های خارجییکی از این تجهیزات که سال 96 آن هم در یک شرکت تبریزی بومی سازی شده، ساخت سرند ارتعاشی بود که پیشتر از هلند و استرالیا وارد می شد.
سرند ارتعاشی جز تجهیزاتی اصلی است که در عملیات تغلیظ مس استفاده می شود و وظیفه اصلی آن در جدایش مواد و دانه بندی آن با ظرفیت 1200 تن بر ساعت است.
این قطعه 8 تنی که ساخت شرکت متسو سوئد بوده و قبلا خرید خارجی می شد هم اکنون در شرکت شیمی پژوهش صنعت تبریز ساخت و در دو مجتمع مس سونگون و مس سرچشمه به بهره برداری رسیده است.
جنس و متریال این سرند از فولاد کربن استیل st52 بوده و در طراحی آن حدود ۴۲۰ پیچ هوک بولت استفاده شده است.
جزء نخستین های بومی سازی شده بعد از اعمال تحریم های آمریکا در داخل کشور است، قطعه ای که هزینه واردات آن با قیمتهای سابق ارز یعنی قبل افزایش ارز، یک و نیم ملیارد تومان بود.
حالا با بومی سازی و تغییراتی که انجام شده قیمت آن به یک پنجم قیمت خارجی کاهش پیدا کرده و جز نمونه هایی است که با نمونه مشابه خارجی خود رقابت می کند.
از این قطعه به طور متوسط سالانه یک دستگاه در مجتمع مس آذربایجان نصب می شود که با داخلی سازی آن حدود ۲۱۷ هزار یورو کاهش ارزبری داشته است.
قطعات بومی، جا پای خود را محکم کرده اندقطعات بومی سازی شده، در پمپ ها، الکتروموتورها و شیرآلات پمپ خانه ی، مجتمع جا پای خود را محکم کرده اند.
پمپ خانه به عنوان یکی از گلوگاههای اصلی خط تولید در مجتمع مس سونگون مطرح است، تا همین چند وقت پیش، تجهیزات آن از خارج وارد می شد، سد تحریم ها باعث شد، تا تامین پمپ ها، الکتروموتورها، شیرآلات و قطعات مورد استفاده در آن با مشکل مواجه شود.
تا این اینکه با ایجاد نهضت بومی سازی، قطعات مورد استفاده در این پمپ خانه یک به یک ایرانی شدند.
یکی از مهمترین این تجهیزات پمپ 450 کیلو واتی است که قبلا از آلمان وارد می شد که اتفاقا نیاز بالایی نیز در پمپ خانه به آنها احساس می شد.
دهقان سرپرست تعمیرات ایستگاه می گوید: این پمپ و قطعات آن صفر تا صد، در سپاهان اصفهان تولید می شوند و نیازی به قطعات خارجی ندارند.
وقفه در تامین قسمتهای ضد سایش این پمپ ها که دائم در معرض سایش بودند، باعث خاموشی ایستگاه می شد؛ اما اکنون با دست یابی به فن آوری تولید آن نه تنها مشکلی از بابت کارکرد این پمپ با قطعه خارجی وجود ندارد، پایداری خط تولید نیز تامین شده است.
شیرفلکه ها و پمپ ها، ایرانی شده اندشیرهای هیدرولیکی پمپ استیشن نیز که سال 96 با دلار 3 هزار تومانی با مبلغ 4 میلیارد تومان از کشورهای آمریکا، فنلاند و مالزی وارد می شد، بومی سازی شده است.
رضوی معاون امور مهندسی و مدیریت انرژی مجتمع مس سونگون با اشاره به اهمیت حیاتی شیرهای هیدرولیک می گوید: در اواخر سال 95 گزارشهایی در مورد اهمیت این شیرهای هیدرولیک تهیه شد و با تائید شرکت مس، اقداماتی در زمینه بومیسازی و مهندسی معکوس شیرهای پمپاژ انجام داده شد، تا اینکه بهمن سال 96 به بار نشست و نزدیک سه سال است که شیر هیدرولیک ساخت داخل کار میکند.
یک نکته مهم در بحث شیرهای هیدرولیک این است که یک گلوگاه حیاتی در فرایند تولید است و در مسیر 10 کیلومتری پمپاژ به سد باطله با درصد جامد 50 و فشار 80 بار قرار گرفته است، این شیرها در تیراژ بالا تولید نمیشوند، سفارشی هستند و در کل کشور چنین شیری کاربرد ندارد و خریدار دیگری وجود ندارد.
در مجتمعهای دیگر شرکت مس، پساب کارخانه بهصورت ثقلی به سد باطله میرود اما در مجتمع سونگون، باطله با هزینههای بسیار زیاد و در شرایط سخت به سد باطله پمپاژ میگردد.
علمی سرپرست عملیات ایستگاه پمپ که مسئولیت نگهداری این شیر فلکه ها را دارد می گوید: نمونه های خارجی این شیر فلکه ها که آمریکایی بودند قبلا هر 6 تا 8 ماه در اثر خورندگی سیال تعویض می شدند، اما نمونه بومی سازی شده، حدود 3 سالی است که اینجا نصب شده و بدون تعویض و نگه داری، ضمن کاهش زمان توقفات و هزینه های نگهداری مورد بهره برداری قرار گرفته است.
عمق ساخت داخل این قطعه به 100 درصد رسیده و با داخلیسازی آن حدود 65 هزار یورو کاهش ارزبری داشته است.
موتوژن؛ موتور سونگون را می چرخاندالکتروموتور اینورتور نیز به سفارش شرکت مس سونگون در شرکت موتوژن تبریز ساخت شده و به این پمپ خانه منتقل شده است، تا جایگزین الکتروموتورهای برزیلی شود.
معاون تولید شرکت موتوژن می گوید: این شرکت با هدف بومی سازی الکترو موتورهای صنایع مختلف به همت کارشناسان خود توانسته این موتور را به سفارش شرکت مس سونگون طراحی و ساخت کند.
به گفته معصمی، صنایع مشابه مس سونگون قبلا این نوع از الکتروموتور ها را از کشورهای اروپایی تامین می کردند؛ موتوری 500 کیلو وات با دور 1000 و قابلیت کار با درایو که هزینه تمام شده آن یک سوم مشابه شرکت های اروپایی است.
این نوع از موتورها، در صنایع سنگین معدن، سیمان و فولاد به کار گرفته می شوند، موتور با دور نامی حرکت می کند ولی این قابلیت را دارد که در دور پایین نیز کار کند.
دستگاه جمع کن نوار نقاله 22CV02 نیز یکی دیگر از تجهیزات بومی شده است که جهت انجام تعمیرات نوار نقاله ساخته شد.
در کمتر از 3 الی 4 ماه در شرکت شیمی پژوه تولید شد، یک طرح ابتکاری محسوب می شود که توانست در مدت 18 شبانه روز، 2 هزار و 400 متر نوار را تعویض کند.
نوار نقاله به طول 2 هزار و 400 متر، قادر است در 24 ساعت حدود 40 الی 45 تن سنگ معدن را از سنگ شکن به کارخانه انتقال دهد، این دستگاه قادر است بار 45 تنی نوار را تحمل کند.
فرصتی برای نفس کشیدن، طرح های ابتکاریدر ادامه همین نهضت بومی سازی برخی طرح های ابتکاری نیز فرصت نفس کشیدن پیدا کرده اند، مثلا دستگاه نوار نقاله کنسانتره مس سونگون ساخت یک شرکت تبریزی که همین چند روز قبل تست نهایی سومین نسخه از آن انجام شد.
نوار نقاله انبار کنسانتره مجتمع مس سونگون یک تجهیز 17 متری است که با همت مشترک تیم مهندسی مجتمع مس سونگون و خدمات بازرگانی منطقه آذربایجان طراحی و کار ساخت آن ظرف 75 روز در شرکت یونار دمیرانجام پذیرفته است.
فرهنگی مدیر عامل شرکت یوناردمیر می گوید: این کانوایر دارای سیستم ویبره و توزین است که در عملیات حمل و بارگیری کنسانتره مس کاربرد داشته و ظرفیت اسمی آن بالغ بر 400 تن بر ساعت است.
عمده جنس و متریال این تجهیز 16 تنی، فولاد کربن استیل st37 بوده و با تکیه بر توان داخلی، تمامی قطعات مکانیکی بکار رفته تولید داخل کشور است.
شرکت یوناردمیر حتی ساخت انواع رولیک برای مس سونگون را نیز در دستور کار خود قرار داده است.
در این زمینه شرکت یونار دمیر که از سال 1369 در زمینه طراحی و ساخت تجهیزات صنعتی آغاز به کار کرده است، پیش قدم شده و هم اکنون سازنده تجهیزات متریال هندلینگ و نخستین تولید کننده رولیک های نوار نقاله با دستگاه های CNC در کشور با ظرفیت تولید روزانه 600 عدد رولیک است که نیاز مس را نیز تامین می کند.
این شرکت در راستای رقابت با تولید کنندگان خارجی اقدام به انتقال دستگاه های تمام اتوماتیک کرده و بابهره گیری از آخرین متدهای تولید انواع رولیک به نوبه خود پیشرو در این صنعت است که با تولید 30 هزار عدد، رولیک در سال 99 یکی از تامین کنندگان اصلی صنایع و معادن از جمله شرکتهای ملی صنایع مس ایران و سایر شرکت های مصرف کننده است.
تنوع سفارشات بسته به کلاس رولیک و بار وارده بر آن طبقه بندی شده و در تولید نهایی، تست های مکانیزه مانند تست عدم نفوذ آب، تست عدم نفوذگرد و غبار، تست لنگی و تست چرخش تحت بار، مورد آزمایش قرار میگیرد.
صنعت مس، به پشتوانه صنایع داخلی، برنامه ریزی می کنداین ظرفیت و توانمندی های صنایع داخلی را در گوشه ای از ذهن خود داشته باشیم، بگذاریم کنار شواهدی که حاکی از آن است که ظرف 4 سال آینده فاز 3 مجتمع مس سونگون با ظرفیت تولید 150 هزار تن کنسسانتره و 100 هزار تن کاتد نهایی خواهد شد، یعنی نیاز به تجهیزات بیشتر و بروزتر احساس خواهد شد.
عبدی مدیر برنامه ریزی شرکت صنایع ملی مس ایران می گوید: این شرکت برای تحقق اقتصاد مقاومتی و مقاوم سازی تولید و نیز تحقق برنامه های توسعه ای، در 3 بخش مقاوم سازی تولید، حفاظت از معادن و بومی سازی قطعات وارد عمل شده است.
به گفته عبدی، شرکت صنایع ملی مس ایران، در بخش مقاوم سازی تولید، با اتخاذ روش های مهم و پیشرفته علمی از تکنولوژی های جدید بهره گرفته است و بر همین اساس تا پایان سال آینده ذوب 300 هزار تن مس را به عنوان بالاترین میزان تولید شرکت ملی صنایع ایران رکورد زنی خواهد کرد و برای سال 1401 ذوب 320 هزار تن را در برنامه خواهد داشت.
شرکت ملی صنایع مس ایران، ضمن مصونیت تولید و حفاظت از معادن در برابر آسیب های احتمالی، بعنوان پیشگام ساخت و بومی سازی تجهیزات مطرح است.
رخنه بومی سازی، تا قلب قطعات نسوز صنعت مسبه گواهی آمار و ارقامی که وجود دارد، شرکت ملی مس ایران، در همه تعمیرات اساسی بیش از 90 درصد قطعات را تعمیر یا تعویض می کند که حدود 80 درصد قطعات مکانیکی و ریخته گری مورد استفاده در داخل کشور تولید می شوند.
عبدی در این باره می گوید: در تامین قطعات سنگین تقریبا یک چهارم تا یک پنجم تجهیزات، در قطعات برقی حدود 60 الی 80 درصد قطعات و در قطعات نسوز مورد استفاده برای کوره های ذوب نیز بیش از 93 درصد بر دوش شرکت های داخلی است.
در شرکت صنایع ملی مس ایران، سالانه یک هزار و 200 قطعه جدید با اعتبار 2 هزار و 500 میلیارد تومان، بعنوان قطعات جدید در چرخه تولید ساخت داخل وجود دارد که در مجموع سالانه از خروج 100 میلیون دلار جلوگیری می کند.
تکاپوی 600 سازنده، برای تامین تجهیزات صنعت مسبرای اینکه این قطعات، نام ایرانی را یدک بکشند، بیش از 600 سازنده مدام در کل کشور کار می کنند.
آنچه در این میان بیش از پیش به چشم می خورد، پر رنگ شدن سهم شرکت های سازنده استانی در گرفتن گوشه ای از کار است.
معاون بازرگانی شرکت مس آذربایجان می گوید: به طور متوسط سالانه 7 هزار قلم کالا برای مجتمع مس سونگون در قالب خرید داخل تامین می شود، اگر نسبت عملکرد سال 99 نسبت به 2 سال اخیر ارزیابی شود، در تامین قطعات مورد نیاز مس سونگون از منطقه، شاهد رشد 200 درصدی هستیم.
براساس آمارهایی که خیرخواه رو می کند:برای تامین تجهیز مجتمع مس سونگون در 11 ماه امسال نزدیک به 5 هزار قلم کالا برای پایداری خط تولید تامین شده است، این میزان از نظرحجمی چیزی معادل 5 هزار محموله تریلی می شود که بطور متوسط روزانه 15 الی 20 تریلر مواد اولیه قطعات و ملزومات خرید بازرگانی وارد مجتمع مس سونگون می شود.
تمامی این کارها با این هدف صورت می گیرد که سیاست های جهش تولید حفظ شود، چرا که پایداری خط تولید برای بازرگانی یک اصل همیشگی است.
با بومی سازی 878 قطعه ای که در 11 ماهه به مجتمع مس سونگون تحویل داده شده است، تعداد 52 سازنده از سازندگان منطقه در تامین این تعداد قطعه مشارکت داشته اند، بیش از 200 میلیارد تومان گردش مالی این قطعات بوده، که فقط 120 میلیارد تومان از این رقم مربوط به تامین گلوله ها است.
اگر این تعداد قطعه از محل خرید خارجی تامین می شد، حتما 3 تا 4 برابر بیشتر از این رقم برای مس تمام می شد.
فقط در بررسی داخلی سازی قطعات خارجی برای مجتمع مس سونگون، در بازه زمانی سال 98 به آمار صرفه جویی ارزی ۶ میلیون یورویی می رسیم.
در سال گذشته یک هزار و 198 قطعه از طریق بازرگانی برای مجتمع مس سونگون ساخت و ارائه خدمات فنی شده است که 868 قطعه از این ارسالی مربوط به ساخت کامل قطعه بوده و 277 قطعه نیز از میان اینها دارای سابقه خرید خارجی بوده که با طراحی و نقشه کشی در دفتر فنی بازرگانی با بهره برداری از توان کارخانجات و شرکت های فنی و دانش بنیان به ساخت داخل تبدیل و به مجتمع تحویل شده است.
به گفته سخاوت خیرخواه عضو هیات مدیره شرکت خدمات بازرگانی معادن و فلزات غیرآهنی و معاون منطقه آذربایجان شرکت مس سونگون تامین داخلی این قطعات به میزان 81 درصد نیز کاهش هزینه داشته است.
رضوی معاون امور مهندسی و مدیریت انرژی مجتمع مس سونگون نیز با اشاره به آغاز نهضت تولید داخل از سال 91، می گوید: سهم استان از حدود 5 درصد به 46 درصد است و هم اکنون از 7 هزار و 500 آیتمی که به عنوان ساخت داخل درخواست شده 5 هزار و 500 قطعه تامین شده است.
او می افزاید: اگر سال 91، یک و نیم میلیارد تومان سهم استان بود سال 99 این عدد به بالای 400 میلیارد تومان می رسد.
بومی سازی 70 درصدی قطعات، در صنعت مسمدیر عامل شرکت خدمات بازرگانی شرکت ملی مس ایران می گوید: از سال 91 تا به امروز در این بومی سازی قطعات مورد استفاده در شرکت ملی مس ایران، رشد 70 درصدی داشتیم.
محمد صابر شاهنوش نیز می گوید: تمرکز شرکت ملی مس ایران و شرکت خدمات بازرگانی که کار پشتیبانی شرکت مس را انجام می دهد بر تقویت ساخت داخل است و در یک دهه گذشته بیش از 40 درصد قطعاتی که در شرکت صنایع ملی مس ایران مورد استفاده قرار می گیرد.
براساس اظهارات این مقام مسئول، در شرکت ملی مس ایران در سال 99 بیش از 16 هزار قطعه بومی سازی و ساخت داخل شده و در سونگون بیش از هزار و 500 قطعه که تا پیش از این خرید خارجی بود، ساخت داخل شده است، چیزی معادل 75 درصد قطعات.
مدیر عامل شرکت خدمات بازرگانی شرکت ملی مس ایران یادآور می شود: در شرکت ملی مس ایران، طی این 10 سال از محل بومی سازی قطعات، بیش از 28 میلیون یورو صرفه جویی ارزی شده است.
کاتد، گرایی جدید به بومی گراییدر طی 10 سال اخیر 6 هزار قطعه مورد نیاز مجتمع مس سونگون، ساخته شده و این در حالی است تنها در 11 ماهه امسال 932 قطعه به همت مهندسان و کارگاههای ساخت، تامین شده است.
این آمارها را گفتیم؛ بد نیست، نگاهی نیز به ظرفیت های تولید در شرکت مس سونگون داشته باشیم، جواهری خفته در سینه آذربایجان.
تولید 300 هزار تن کنسانتره در سال، به مدد فعالیت دو کارخانه تغلیظ است که با آغاز بکار فاز 3 تولید کنسانتره در این مجتمع، 500 تن در روز به ظرفیت تولید کنسانتره اضافه خواهد شد که در سال 150 هزار تن خواهد بود.
این مجتمع، در کنار تولید کنسانتره، تولید کاتد را نیز در برنامه دارد که شامل 4 طرح ذوب، پالایش، اسیدسولفوریک و اکسیزن خواهد بود.
در 3 سال آینده چیزی حدود 20 هزار میلیارد تومان سرمایه گذاری در منطقه صورت خواهد گرفت، که قطعا این سرمایه گذاری در اقتصاد کشور، اقتصاد منطقه و همچنین اشتغال منطقه سهم بسزایی خواهد داشت.
آری برنامه ای که قرار بود، صنعت مس را زمین گیر کند و چرخ های این صنعت را بخواباند، جور دیگری ورق خورد و هم اکنون این چرخ ها با توان بیشتری می چرخند، آن هم بی هیچ وقفه ای؛ و تولید را فقط در مس سونگون نسبت به سال قبل 5 درصد افزایش داده اند.
گزارش مکتوب از : اعظم قربانی ـ خبرگزاری صداوسیما ـ تبریز